Cutting-edge Fads in Steel Construction: Enhancing Sturdiness and Accuracy
In the realm of steel fabrication, the quest of toughness and accuracy has led to a wave of ingenious trends that are improving the industry. From advancements in welding innovations to the integration of robot automation in construction procedures, the landscape of steel production is evolving quickly. High-strength alloy growth, coupled with the usage of 3D modeling and simulation software application, is pressing the borders of what is achievable in regards to structural integrity and precision. The growing emphasis on lasting practices in steel production is not only driving efficiency however additionally cultivating a much more ecologically aware method to construction. These patterns are not just forming the existing yet also preparing for the future of steel fabrication, assuring more enhancements in durability and accuracy.
Advanced Welding Technologies
In the realm of steel construction, the fostering of sophisticated welding modern technologies has considerably transformed the market's approach to accomplishing premium top quality and precision in architectural welds. Advanced welding technologies, such as laser light beam welding and rubbing mix welding, have actually arised as game-changers in the field. Laser beam welding uses a focused laser light beam to join metal components with remarkable accuracy and rate, making it optimal for thin products and detailed styles. On the various other hand, friction stir welding produces extremely strong bonds by mechanically intermixing the particles of the products at the joint, removing the need for melting the metal. These technologies offer various benefits, including decreased heat-affected areas, marginal distortion, and boosted mechanical residential properties in the bonded joints. By leveraging these innovative welding methods, steel makers can elevate the toughness, toughness, and precision of their structural welds, meeting the increasingly requiring requirements of contemporary building jobs.
Robot Automation in Fabrication
Embracing robotic automation has come to be a keystone of modern-day steel fabrication techniques, enhancing and improving processes effectiveness throughout the industry. Robotics are reinventing the means steel components are produced, using unrivaled precision and speed while minimizing human mistake. These automated systems can take care of repetitive tasks with regular precision, leading to better final result.
One secret benefit of robot automation in steel fabrication is the ability to work around the clock without fatigue, dramatically enhancing production output. This constant operation reduces downtime and increases project timelines, ultimately saving costs for suppliers. Furthermore, robotics can be set to do complex jobs that may be challenging or unsafe for human employees, enhancing security in the work environment.
Moreover, robotic automation enables smooth integration with other electronic technologies, such as computer-aided layout (CAD) software and Net of Things (IoT) systems (Alpha reo). This interconnected method boosts interaction between various stages of construction, maximizing operations and guaranteeing real-time surveillance and control. As the steel construction market proceeds to evolve, robotic automation sticks out as a transformative pressure driving performance and accuracy in manufacturing processes
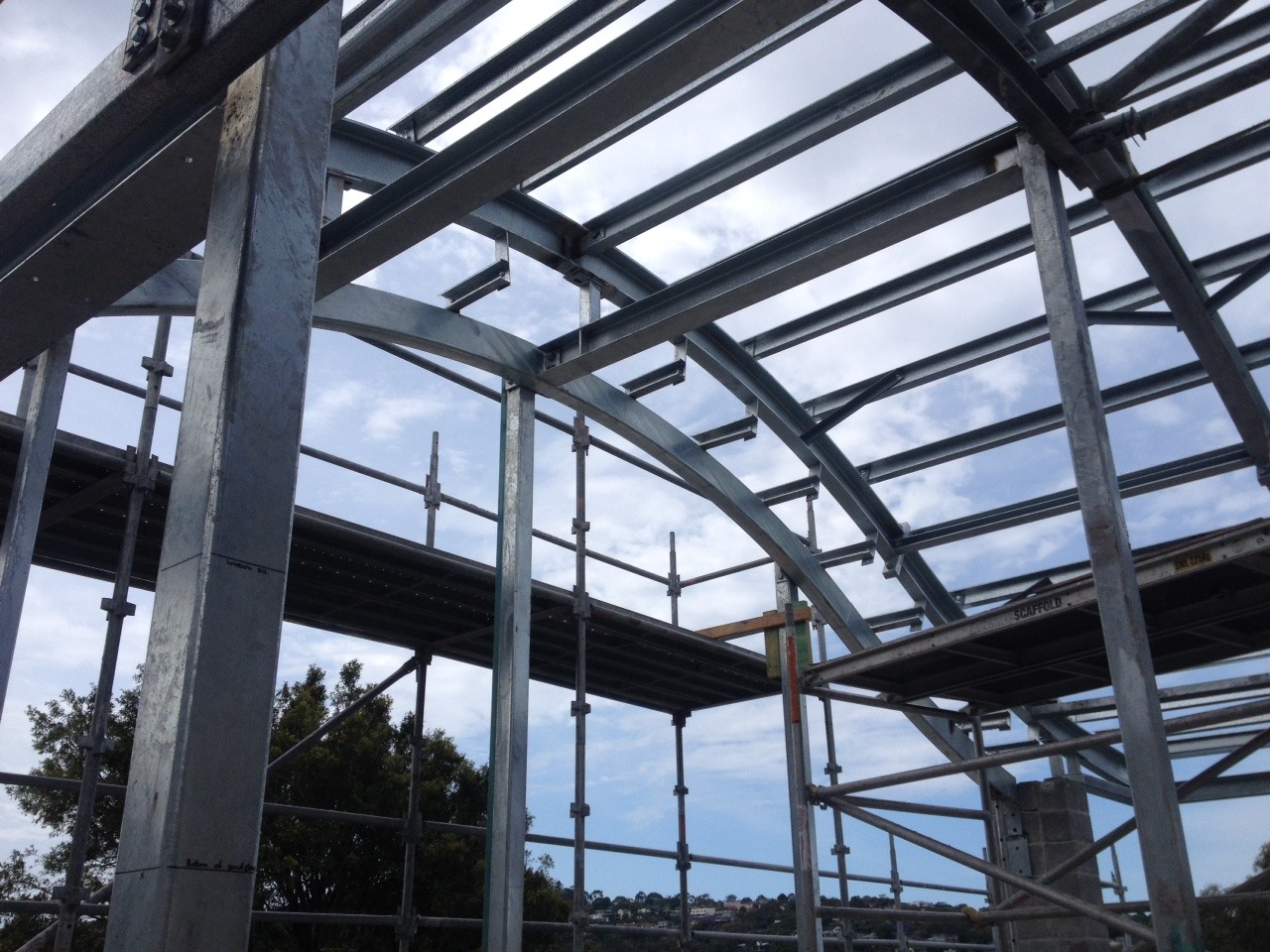
High-Strength Alloy Development
The advancement of high-strength alloy development in steel fabrication is reshaping the sector's approach to enhancing product durability and performance. High-strength alloys are crafted to exhibit remarkable mechanical buildings, such as raised tensile toughness, sturdiness, and deterioration resistance contrasted to typical steel qualities. By integrating these sophisticated alloys into fabrication processes, producers can produce components that hold up against greater anxiety degrees and extreme atmospheres, resulting in more trusted and resilient final result.
One trick advantage of high-strength alloy development is the capacity to lower material thickness without endangering structural integrity. This not just leads to lighter-weight components yet likewise adds to set you back savings and improved performance in construction and setting up processes. Moreover, the boosted strength-to-weight ratio of these alloys enables the style and construction of frameworks with higher load-bearing abilities while minimizing total weight.
3D Modeling and Simulation Software Program
Advancements in steel construction processes have been substantially driven by the assimilation of sophisticated 3D modeling and simulation software application devices. These devices permit fabricators to more helpful hints create comprehensive digital versions of their jobs, allowing them to envision the last item with accuracy before any kind of physical work starts.

Sustainable Practices in Steel Manufacturing
Including lasting practices into steel production processes is essential for decreasing environmental impact and ensuring lasting resource availability. One vital sustainable practice is the fostering of energy-efficient innovations to decrease greenhouse gas discharges during the steel manufacturing procedure. This includes using renewable resource sources, such as solar or wind power, to power steel plants and carrying out energy-efficient devices to enhance energy usage.
One more vital element of lasting steel manufacturing is the accountable sourcing of basic materials. This entails making sure that the iron ore and other sources made use of in steelmaking are obtained from honest and eco-friendly resources. By advertising openness in the supply chain and sticking to rigorous ecological criteria, steel manufacturers can minimize the unfavorable effects of resource extraction on regional ecological communities and areas.
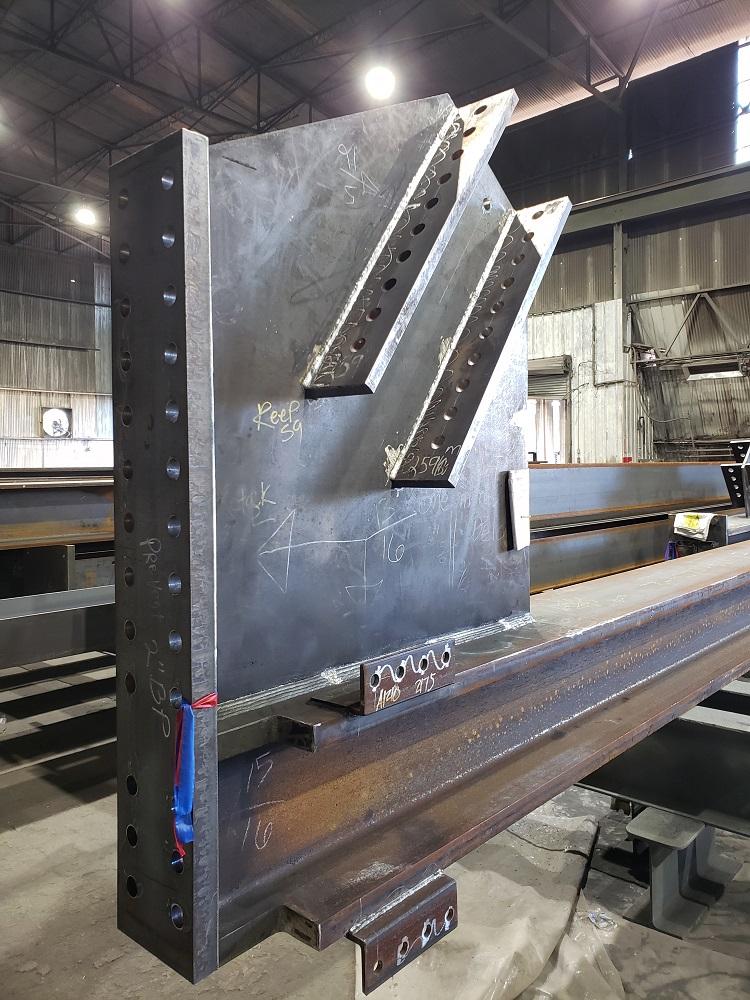
Conclusion
To conclude, the ingenious patterns in steel fabrication such as innovative welding innovations, robotic automation, high-strength alloy advancement, 3D modeling and simulation software application, and sustainable techniques are improving the sturdiness and precision of steel items. These developments are revolutionizing the steel fabrication sector by enhancing efficiency, high quality, and sustainability. It is clear that the future of steel construction hinges on welcoming these advanced modern technologies to satisfy the needs of contemporary building and construction and manufacturing sectors.
In the realm of steel manufacture, the pursuit of longevity and precision the original source has actually led to a wave of innovative patterns that are improving the industry.In the realm of steel manufacture, the adoption of cutting-edge welding modern technologies has dramatically transformed the sector's approach to attaining premium quality and accuracy in structural welds. As the steel manufacture industry continues to progress, robot automation stands out as a transformative pressure driving efficiency and accuracy in producing processes.
Moreover, reusing and reusing steel scrap and waste products play a considerable duty in boosting the sustainability of steel production. Alpha reo.In final thought, the ingenious fads in steel manufacture such as innovative welding technologies, robot automation, high-strength alloy development, 3D modeling and simulation software, and sustainable practices are improving the toughness and accuracy of steel products